Motivation and objectives
Monomaterial components are reaching their material and production-specific limits. For this reason, the manufacturing of hybrid components is investigated in research. The forming production of these workpieces usually requires a machining post-processing. However, this represents a challenge for the machining of the material combinations and for the monitoring of the process. Without adjusting the process parameters, no economic machining process can be guaranteed for two different materials. Furthermore, it is not possible to guarantee surface quality and dimensional accuracy for hybrid components without adjusting the process parameters. The objective of the second research period is to guarantee process capability and process reliability in the machining of hybrid components, which are influenced by production variances in previous production steps, based on cross-process information transfer. The aim is to achieve a "high level of automation" corresponding to the levels of automation of production processes. In this context, relevant product characteristics are controlled by adaptation to changed environmental conditions and tasks, defined error patterns are eliminated and system limits are identified.



Results
In the first research period, new machine and process control technologies for the production of material compounds were researched. For this purpose, the potentials of material-specific adaptation of the process parameters were evaluated on the basis of hybrid workpieces. It was shown that the component and manufacturing quality that can be achieved for material compounds depends on the material combination. Characteristics such as the square mean value were extracted from the process signals and methods were developed to evaluate these with regard to their suitability for monitoring hybrid workpieces. It could be shown that characteristics correlating with the process force have a high sensitivity. Based on this, different methods for monitoring materials for turning, milling and drilling operations were developed and compared. With the predictive process parameter adaptation, a method is available to use the new information and to limit the process forces during the machining of hybrid components as well as to increase the process limits. In order to generate production-independent features for monitoring hybrid components, a feeling tool turret was developed. This allows to measure process forces for turning, milling and drilling processes and to transmit them to the process monitoring with regard to material identification. The influence of hybrid components on process error sensitivity within machining was investigated for a process monitoring approach based on envelope curves. It was shown that the sensitivity of the monitoring algorithms to monomaterial components decreases due to the material compounds.

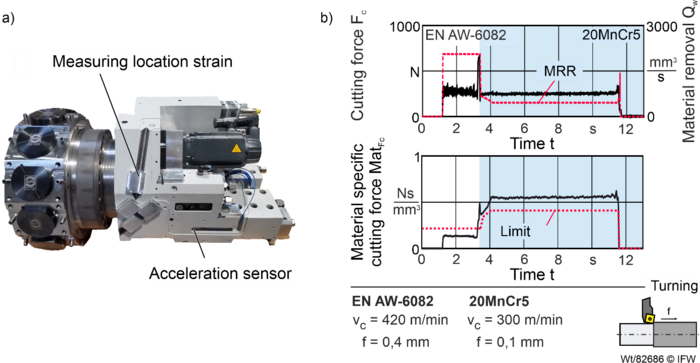
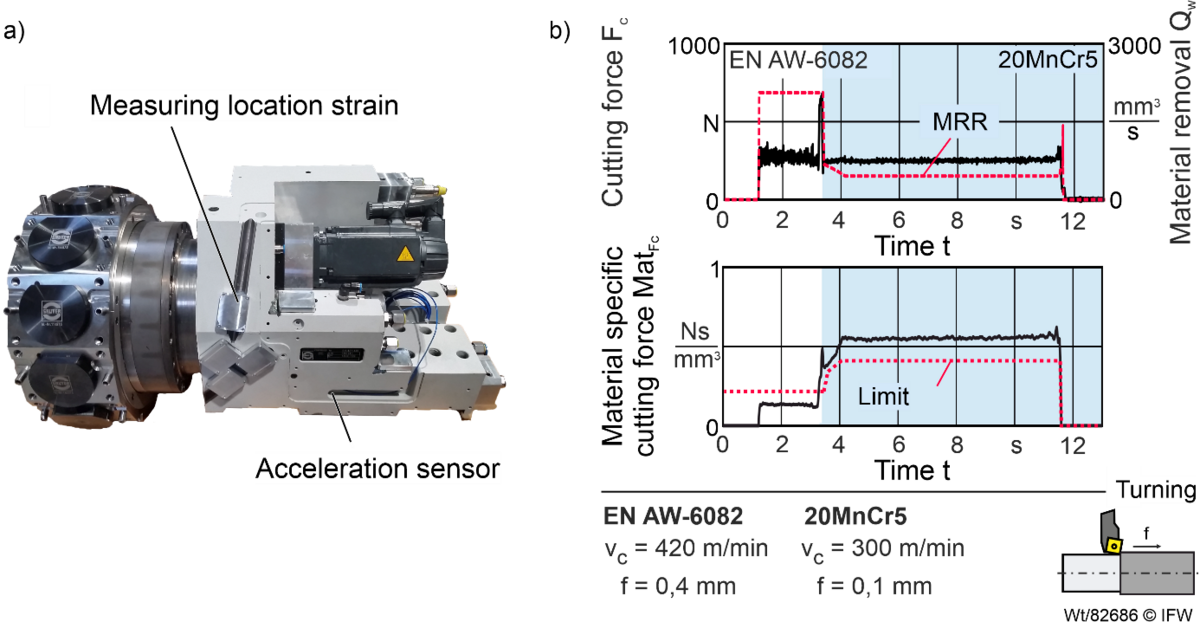
Current work and outlook
The sensitivity of process signals from machining to product-specific manufacturing inaccuracies, such as the variation of material properties, is currently being researched by means of parameter studies and correlation analysis. Information transfer is achieved by creating a database and merging the process information from the different sub-processes. A common semantics for a later classification and common interfaces as well as a data structure will be defined. Together with manufacturing data from previous subprojects of the process chain - process parameters and process signals - the potential of a classification of manufacturing inaccuracies is determined. This offers the possibility to identify inaccuracies at an early stage and to assign the origin to the individual sub-processes. A neural network is used to link the production data with the measurement signals recorded during the machining of tailored forming components. Based on the machine learning process, the process monitoring limits are adapted by manufacturing data from previous manufacturing steps and the material-specific adaptation of the process setting variables is taken into account during monitoring. The component-specific machining is thus supplemented by a component-specific evaluation of the process. The process controllability of the individual production routes is researched for defined product characteristics. For this purpose, a process capability analysis for the individual process routes is carried out based on the measured information, e.g. the position and characteristics of the material transition. The robustness of the cross-process information transfer is guaranteed by identifying faulty data by means of cluster analysis and subsequently correcting it by taking into account the neighboring data points.
Publications
Subproject leader
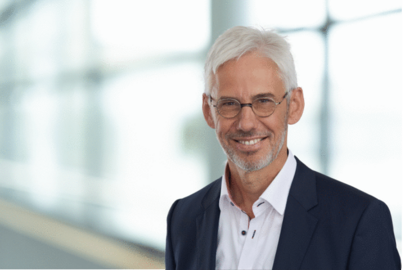
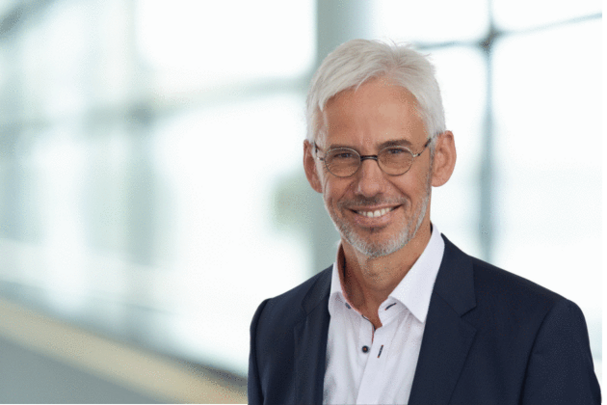
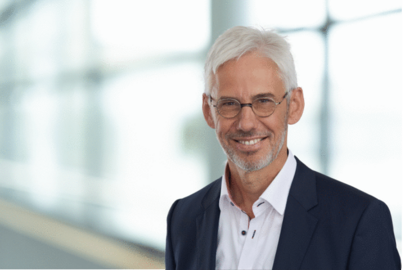
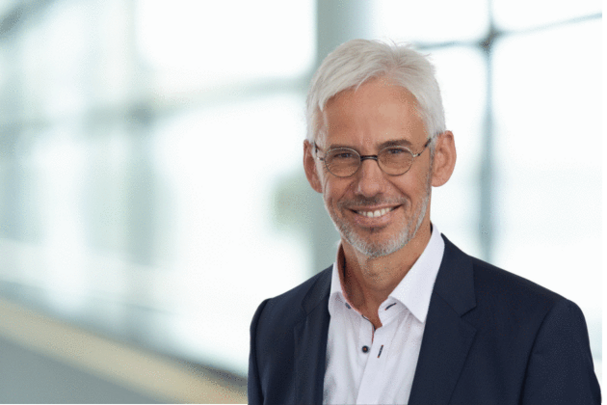
30823 Garbsen
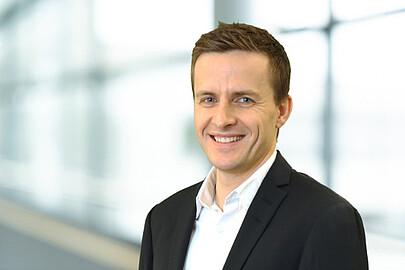
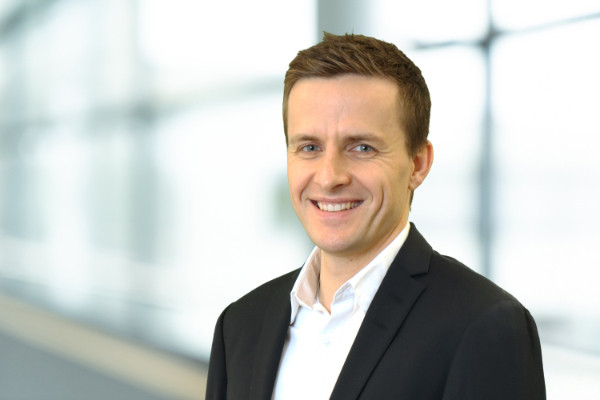
30823 Garbsen
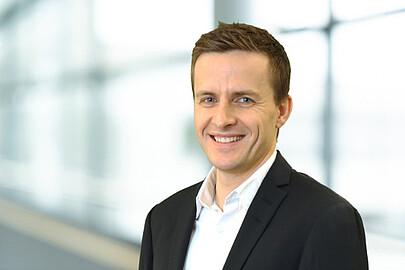
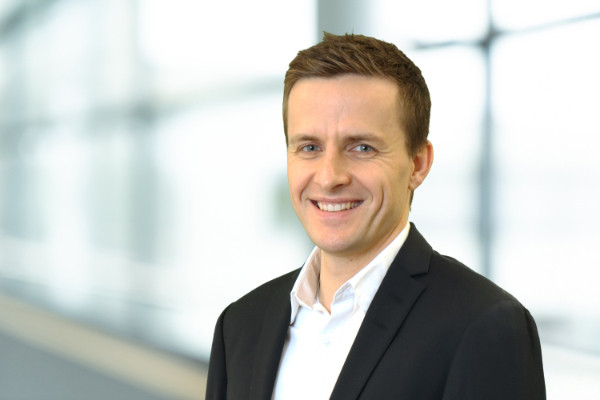
30823 Garbsen
Staff




30823 Garbsen