Motivation und Zielsetzung
Die methodische Grundlage für die Gestaltung und Dimensionierung von Tailored-Forming-Bauteilen ist ein Systemansatz, der die wechselseitigen Beziehungen der Tailored-Forming-Prozesskette betrachtet, Anforderungen und Qualitätskriterien erfüllt und Möglichkeiten sowie Grenzen der Tailored-Forming-Technologie berücksichtigt. Ausgangsbasis des Teilprojektes C02 ist die wissenschaftliche Fragestellung, wie Tailored-Forming-Bauteile konstruiert werden müssen, um das Einsatzpotential hybrider Massivbauteile ausschöpfen zu können. Ziel ist es, Methoden zu entwickeln, mit denen auf der einen Seite der Einsatzbereich der Tailored-Forming-Bauteile vergrößert und auf der anderen Seite der Entwicklungsaufwand für die Prozesskette minimiert wird. Zur Erreichung dieser Ziele wird untersucht, in welcher Form sich geometrisches und fertigungsprozessbezogenes Wissen in die bestehende Entwicklungsumgebung implementieren lässt, sodass dieses zur Informationsrückführung in die Prozesskette verwendet werden kann. Zur Validierung der entwickelten Methoden ist geplant, die am IPeG entwickelten Prüfstände zu nutzen, bzw. weiterzuentwickeln.
Ergebnisse
In der ersten Förderperiode ist mit TRIZ-Reverse eine Methode zur Potentialbestimmung von Tailored Forming entwickelt worden. TRIZ-Reverse basiert auf der Theorie des erfinderischen Problemlösens (TRIZ). Die Methode verwendet die Mechanismen der verallgemeinerten Lösungsprinzipien und der Widerspruchsauflösung. Es wurde untersucht, welches Potential der Einsatz unterschiedlicher Werkstoffe in einem Bauteil im Vergleich zu einem Mono-Material-Bauteil besitzt. Aus den gesammelten Erkenntnissen ist eine Wissensbasis in Form eines Konstruktionskataloges aufgebaut worden, in dem die Potentiale verschiedener Schmiedebauteile für den Tailored-Forming-Einsatz strukturiert gesammelt und ausgewertet worden sind.
Zur Bestimmung der Werkstoffverteilung ist die Topologieoptimierungsmethode Interfacial Zone Evolutionary Optimization (IZEO) entwickelt worden. Die Methode (Abbildung C2.1) ermöglicht es, unter der Berücksichtigung von Fertigungsrestriktionen Entwürfe von Tailored-Forming-Bauteilen zu erstellen.
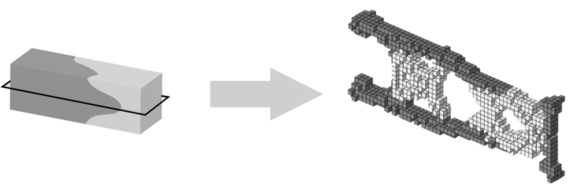
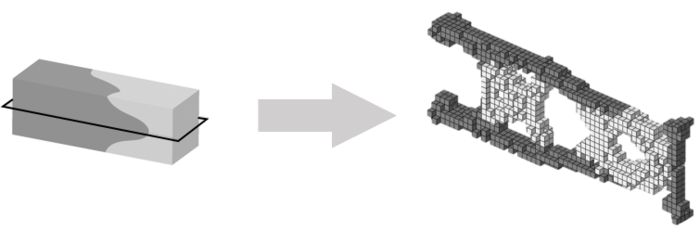
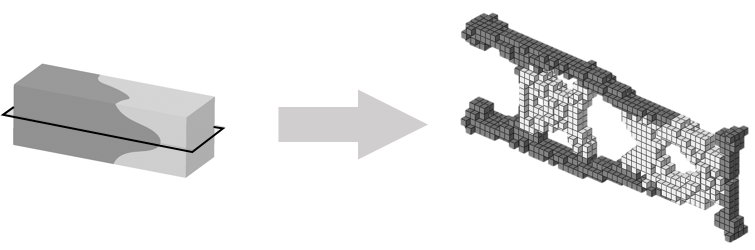
Mittels Parameterstudien sind Gestaltungsrichtlinien für die Fügezonengeometrien von reibgeschweißten und fließgepressten Wellen erstellt worden. Dabei sind sowohl die Fertigungsmöglichkeiten der Prozesskette berücksichtigt worden, wie auch die Ergebnisse, die am entwickelten Torsionsprüfstand (Abbildung C2.2) mit hergestellten Tailored-Forming-Wellen erzielt worden sind.
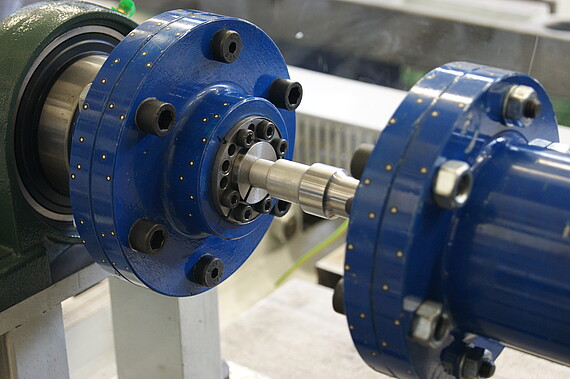
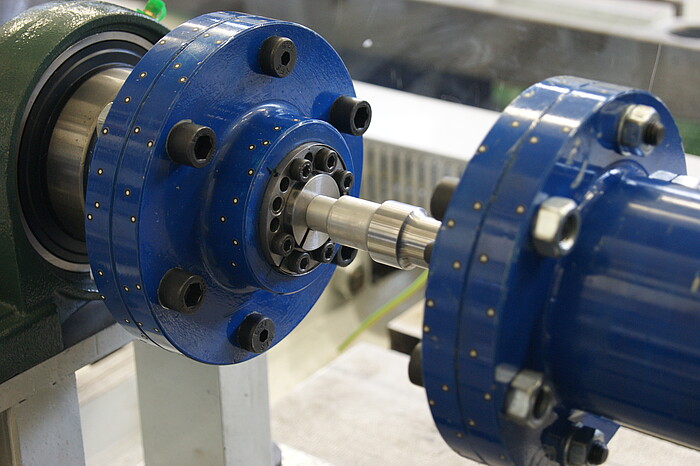
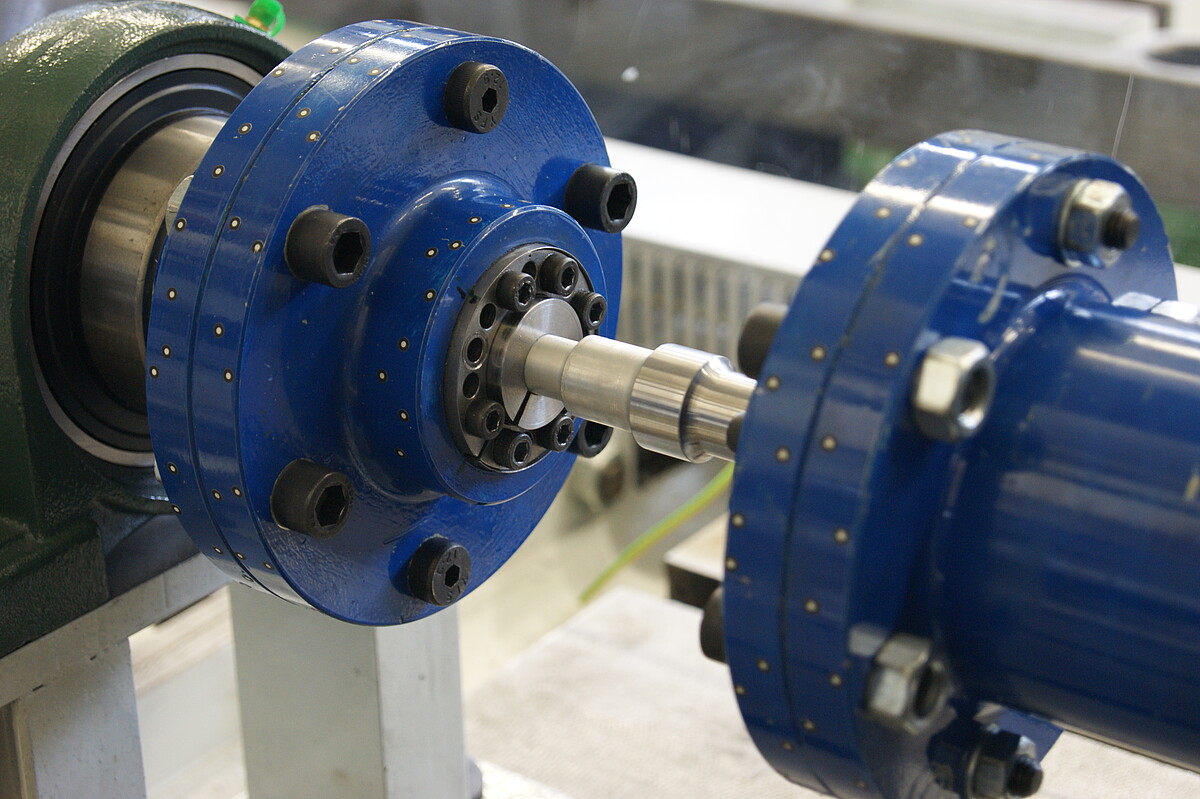
Aktuelle Arbeiten und Ausblick
In der zweiten Förderperiode wird an einer Umsetzung von IZEO für nicht-symmetrische Tailored-Forming-Bauteile gearbeitet, mit der unter anderem die Werkstoffverteilung im Demonstrator Querlenker ausgelegt wird. Zur Validierung der Simulationsmodelle wird ein multiaxialer Belastungsprüfstand in Betrieb genommen (Abbildung C2.3).
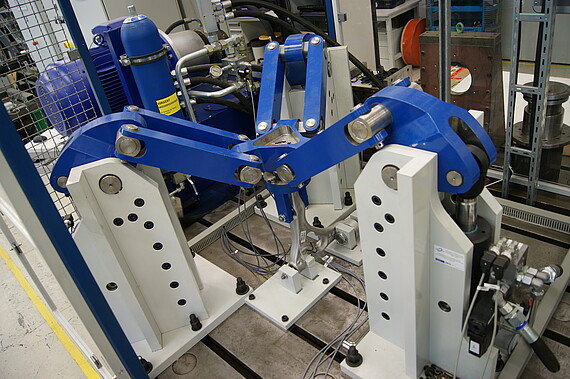
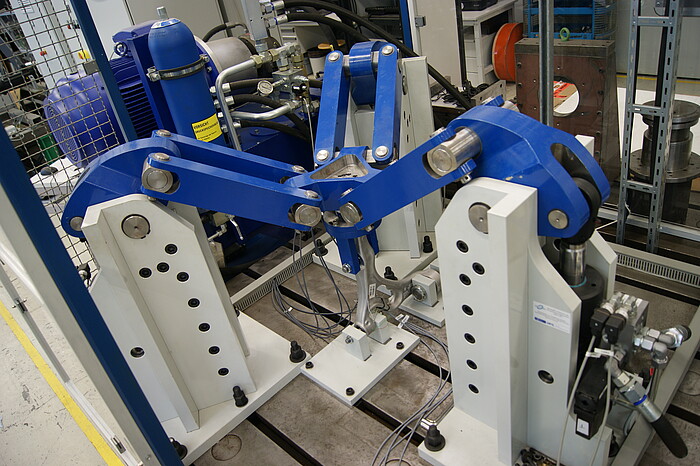
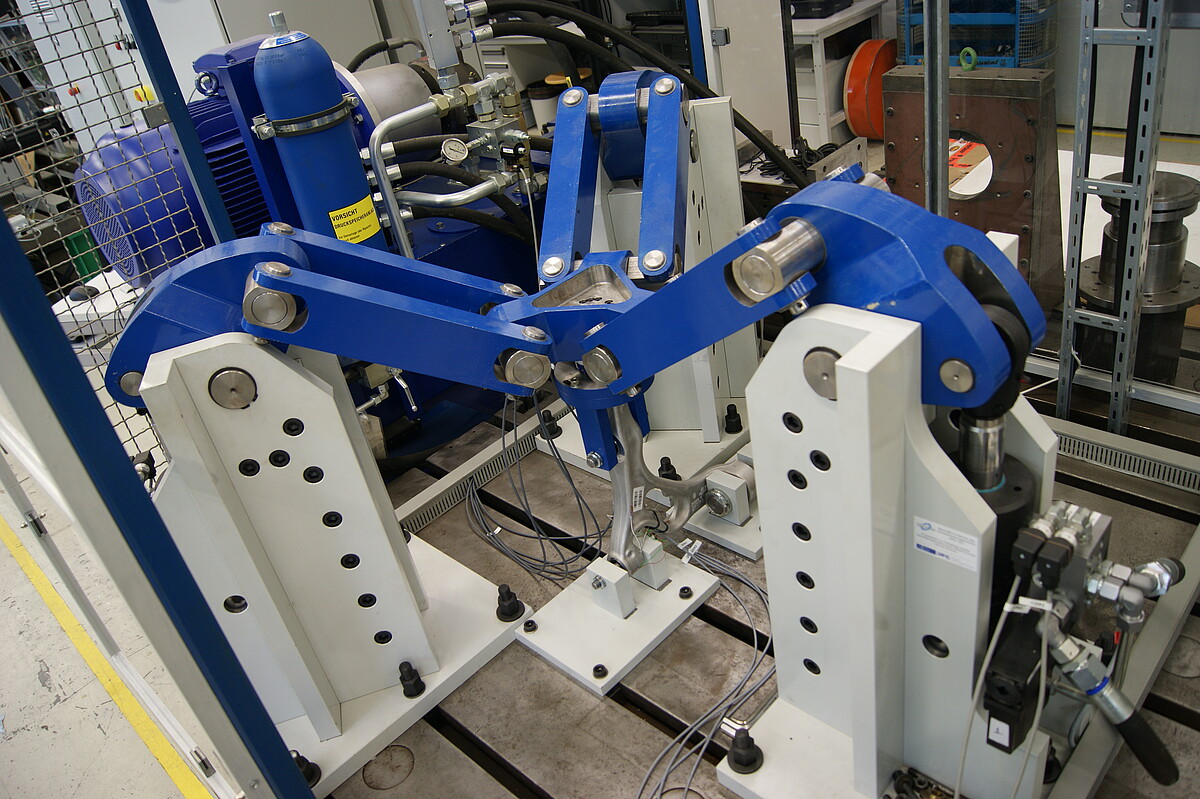
Zusätzlich werden die einzelnen Fertigungsstufen der Tailored-Forming-Prozesskette betrachtet. Es werden verschiedene Transfermodelle aufgebaut, mit denen ausgehend von der finalen Bauteilgeometrie die Geometrie der einzelnen Fertigungsstufen bestimmt werden kann (Abbildung C2.4). Darüber hinaus kann durch die Analyse eines Tailored-Forming-Bauteils auf die Synthese weiterer Bauteile geschlossen werden. Dadurch wird frühzeitig erkannt, ob ein Bauteil mit den zur Verfügung stehenden Mitteln herstellbar ist. Gegebenenfalls lassen sich die zur Herstellung benötigten Geometrien der Umformwerkzeuge aus den Modellen automatisiert ableiten.
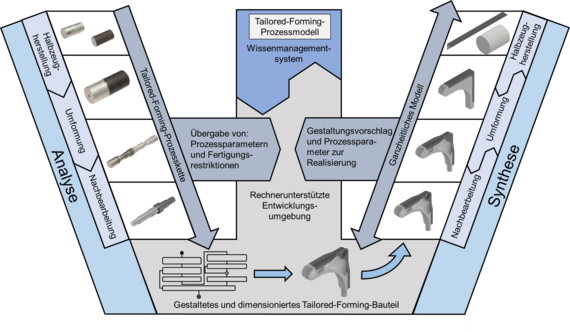
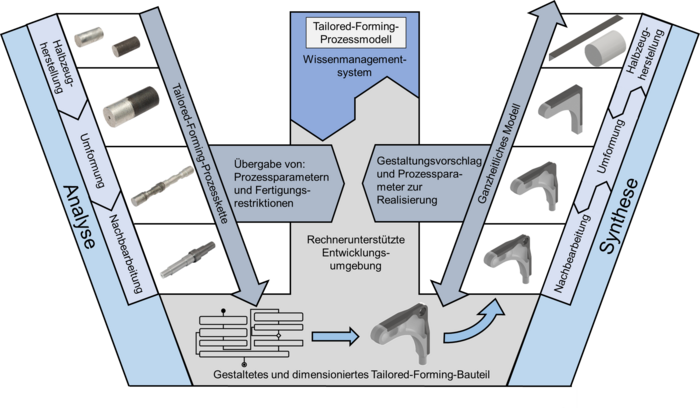
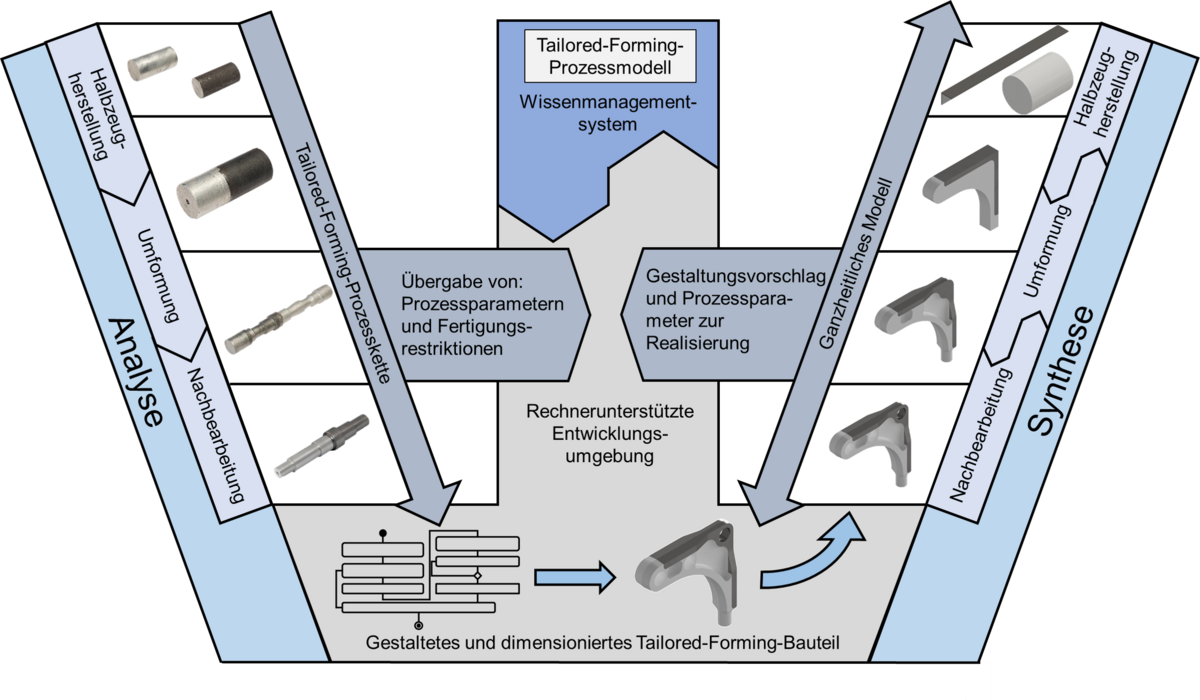
Veröffentlichungen
Teilprojektleitung


30823 Garbsen


30823 Garbsen


30823 Garbsen


30823 Garbsen
Teilprojektbearbeitung


30823 Garbsen


30823 Garbsen